This factory produces interior and exterior parts for passenger vehicles, buses, lorries, tractors, agricultural and construction machinery, installed in vehicles: Zastava, Ikarbus, FAP, IMT, Casalini, Breda and VDL buses.
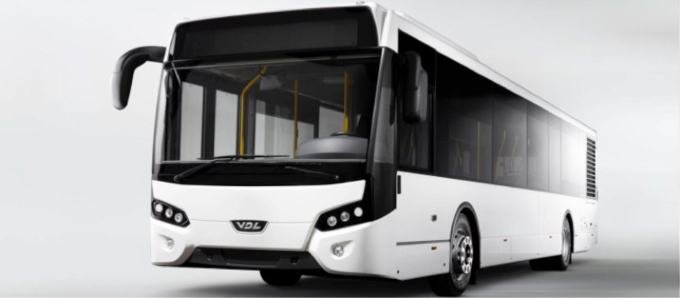
Dozens of different products are manufactured for automotive industry, such as: dashboards, bumpers, masks, spoilers, wheel arches, footsteps, tractor hoods, wheel arches, car battery cases, interior covering, thermal and sound insulation, arm holders, glove compartments, handles, seat fillings etc.
The factory produces plastic dishes (bowls, cups, glasses, plates, trays, etc.), plastic packing material (crates for raspberries and blackberries, crates for mushrooms, crates for beverages and beer), plastic targets and other plastic products for dedicated - military industry.
Quality of these products is guarantied by extended experience and cooperation with all domestic, and several international manufacturers. The factory has introduced quality assurance system according to ISO 9001:2001 and introduction of automotive Industry Standard TS 16949 is pending.
Several production methods are used:
- vacuuming ABS foils, PS (poly-styrene) plates, ABS plates and PMMA/ABS (poly-methyl-meta acryl) plates; thickness up to 3,5 mm. The Parts obtained with this method can be hardened with PUR foam or GFK material, and they can also be used individually, mainly for the needs of automotive industry.
- injection of PE (poly-ethylene) and PP (poly-propylene), is used to manufacture products of wide application range: crates, buckets etc; while ABS, PC (poly-carbonate) and PA6 (polyamide 6) used to manufacture parts for technical applications: handholds, latch parts, protection of slippery surfaces etc. Parts obtained by injection process are between 45 g and 2 kg in mass.
- processing of previously prepared material, polyester resin and chopped roving, is used for manufacture of SMC products. By applying high pressure and temperature, polymerisation occurs. Parts obtained with this method are used in wide range of applications. These products excel at great firmness, guarantied mechanical properties, high gloss, and excellent resistance to atmospheric conditions.
- polymerisation of polyester resin reinforced with glass fibre or matt is used for manufacture of GFK parts. This technology is extremely worthwhile for large dimensions products in small series with optional finishing and painting in level with metal sheets. Finishing can be in gelcoat, painting with nitro colour, PUR colour, or acrylic colour, and metallic finishing surface can also be obtained.
- mixing components in high pressure machine is used for production of soft PUR foam. By moulding this material, cold shaped parts with different density and hardness are obtained depending on customer’s demands. Parts can be upholstered with the leather, leatherette, linen or other materials depending on application. Upholstered parts are used in automotive and railway industry, and seats and backseats for air industry can be produced using the same technology. Semi hard foam combined with the other materials is used in production of dashboards, roof coverings, door coverings, and different kinds of thermal and sound insulation, as well. Polyurethane, integral foam, thick crust (cca 600 kg/m3) and core density cca 300 kg/m3 is used for products resistant to wearing and tearing: handholds, arm holders, steering wheel coverings, tractor seats, back seats etc. No upholstering is needed, and the product can be engraved in a certain pattern.
Autooprema Factory can also manufacture wood or epoxy resin models in its workshop, as well as tools for vacuuming and for production of PUR foam and GFK parts.